anodizing seal test 35 or 50|anodized aluminum test : dealer This article presents a historic review with some of the issues concerning the MIL-PRF-8625F abrasion test that still need to be addressed and how the September 2022 publication of ASTM B1023 – Standard Test Method .
WEBBatman & the Joker Jewels is the fruit of a deal that has also delivered Man of Steel, Superman II and Green Lantern games. Let’s take a closer look at this action-packed, .
{plog:ftitle_list}
21 de fev. de 2024 · 受付時間: 00:00〜24:00 年中無休 [email protected] 「顧客起点で品質を追求し、お客様を大切にする」という永遠に変わらない基本理念を遵守し、通信販売を通じて、高品質・低価格・安全・安心な商品をお客様にご提供いたします。

The most common of these test methods include film thickness measurement, the seal of anodic coatings, and conductivity measurement. Knowing the basics of each method and the influences that affect each .Seal Test. ASTM B 136 - Standard* method for measurement of stain resistance of anodic coatings on Aluminum. 1.1. Scope. 1.1 This method is intended to determine whether anodic . The easiest to do is hot water seal. Use distilled or demineralised water with a conductivity below 150 microsiemens and a pH of about 6 (5.5-6.5 is not uncommon). Seal for .
Basically a 50% nitric acid is applied to a small area (drop or two) of the part and left on for 6 minutes after which it is wiped with a clean damp cloth. A Blue dye is then applied for a . The best test you could is to dissolve a dark dye in oleic acid (the same present on your finger) and put a drop of it onto the anodised surface and remove it with a shower tap. You can graduate the effects of greasing letting a . This article presents a historic review with some of the issues concerning the MIL-PRF-8625F abrasion test that still need to be addressed and how the September 2022 publication of ASTM B1023 – Standard Test Method .
The sealing step is an important step employed in the aluminum anodization process principally to preserve the aesthetics [1] and improve the corrosion resistance of the anodized aluminum by ensuring that the pores of .A destructive test for ascertaining seal quality (and coating weight if necessary) utilizes a solution of chromic and phosphoric acids at selected temperatures. Because it dissolves the film but .
A cold seal — also known as a room-temperature seal — is a sealing bath that contains nickel and fluoride and is used at ambient temperatures. The best results are obtained with temperature regulation, . Anodizing aluminum is an electrochemical process that produces a wear-resistant, corrosion-resistant aluminum oxide coating on the surface of aluminum parts. . Step 4: Seal. To seal the porous surface created during . In conversations with our anodizer on the best way to seal parts for adhesion prior to painting, he referred to a choice of either a final hot water immersion at around 120°F with no seal or a hot water seal at a much higher temperature. . Hubbard-Hall has remained a steadfast partner standing the test of time by building on family legacy .
anodized aluminum test
Sealing of anodized aluminum is considered the most important of the various steps in the anodizing process. How you seal determines the performance of the anodic oxide in its end-use environment. Depending on the projects you expect to undertake in your new line (and of course availability of space), you could consider having multiple sealing . Hard Coat anodizing provides high wear resistance, typically scoring a weight loss of 1.0-1.5 mg/1000 cycles in the ASTM D4060 abrasion resistance test. Regular anodizing offers moderate wear resistance, scoring a weight loss of about 20-35 mg/1000 cycles in the same test. Corrosion Resistance Anodizing an aluminum part will lead to surface growth – outer diameters get bigger and the hole smaller – due to the aluminum oxide layer. The extent of deposition of the coating depends on the type of anodization. However, it is estimated to be approximately 50% of the anodic layer’s total thickness. In industrial practice the three common tests used to evaluate sealing quality are: (a) The dye spot test in which the qualification criterion is a spot strength below 2 [183,184]; (b) the phosphor-chromic acid dissolution test in which the allowed mass losses should be below the threshold value of 30 mg/dm2 of sample surface [185,186,187]; (c .
Anodized coatings range in thickness from 8-16 μm, or up to 35-50 μm for hardcoating. . Seal the pores. After anodizing, you have to seal the microscopic pores on the surface of the part to prevent further corrosion and improve performance. . To assess the quality of anodization, you should test how resistant the part is to abrasion and . Conductivity test: For this test you only need an ordinary voltmeter. Anodized aluminum parts have a lower conductivity. Oxide layer: Anodizing will produce a layer of aluminum oxide with a thickness of 5~25um on the surface of aluminum parts, and the thickness is more uniform in each place. This is also a way to identify.
Additionally, post-anodizing inspections and tests should be conducted to verify the integrity of the seal. 7. 5 Tips for Maintaining Anodized Titanium Products. After addressing common problems and solutions in anodizing titanium, let’s now shift our focus to .
The "stain resistance test" as we call it can be found in detail in the ASTM document titled ASTM B136 "Measurement of stain resistance of anodic coatings-test method" Your local Document center should have this. Basically a 50% nitric acid is applied to a small area (drop or two) of the part and left on for 6 minutes after which it is wiped with a clean damp cloth. The authoritative public forum for Metal Finishing since 1989 -----Spot type seal check for black anodized aluminum. Q. Why black anodized part shows dark spot after nitic acid spot test (ASTM 136 ^ ASTM B136)?Just place a nitirc acid (50% volume) drop on anodized part for 2 minutes.Anodizing is an electrolytic passivation process used to increase the thickness of the natural oxide layer . Thicknesses of up to 50 μm can be achieved. Organic acid anodizing is called Type IC by MIL-A-8625. . nickel acetate, cobalt acetate, and hot sodium or potassium dichromate seals are commonly used. MIL-A-8625 requires sealing for .
A rule of thumb is 50-50 penetration vs. build: about one thousandth of an inch of aluminum is consumed in building a coating thickness of two thousandths. Reference Materials The most in-depth reference on anodizing is doubtless The Surface Finishing and Treatment of Aluminum and its Alloys [adv: suggestions on AbeBooks , Amazon & eBay affil . We have some parts that we send out for anodizing per MIL-A-8625 / MIL-PRF-8625 [on DLA]. They are also required to be sealed. . There is an ASTM test, ASTM B136, which is similar to the dye test you are running, except a 50:50 nitric acid solution is applied to a flat surface for 2 min., washed off, . Those who are more serious about seal .
Anodizing is a critical process in enhancing the durability, aesthetic appeal, and corrosion resistance of aluminium. This comprehensive guide aims to explore the specifics of chromic acid anodizing, a method widely used in the aerospace and defense industries due to its superior protection and minimal impact on the material’s mechanical properties.Type I - Chromic acid anodizing, conventional coatings produced from chromic acid bath (see 3.4.1) Type IB - Chromic acid anodizing, low voltage process, 22±2V, (see 3.4.1) Type IC - Non-chromic acid anodizing, for use as a non-chromate alternative for Type I and IB coatings (see 3.4.1 and 6.1.2)
anodized aluminum sealant
5. Activate test coupons with 15-30 second nitric acid dip 6. Dye test coupons in dye solutions and compare depth of color of operating bath to standard bath 7. Test operating dye bath for buffer solution, make correction if required 8. Re-test coupon dyeing in . In addition to what Peter M. advised, anodizing probably is more gravel-resistant than powder coating. But anodizing (and most inorganic coatings) will not pass a 1000-hour salt spray test designed for organic coatings. One third of that, 336 hours, is a fairly standard test for anodized coatings on test coupons.Alternative to conventional aluminum anodize seals with an environmentally friendly seal process Harish Bhatt, METALAST International, Inc. Minden, NV 89423 Sealing of an anodized surface is a standard practice to complete anodizing process and finish. There have been various seal processes that use hot deionized A comprehensive look at the science behind anodizing aluminum, exploring the challenges inherent in the process and its various industrial applications. . This process transforms the aluminum oxide into boehmite, a hydrated form of alumina, which seals the pores and boosts corrosion resistance. . Interpreting test results and making data .
Good anodizing can achieve around 600 volts per mil of thickness. Some proprietary coatings such as Semano’s AX200 coating can achieve around 1200 volts per mil with the total insulation over 4000 volts. Compensating for Anodize Dimensional Change: You can typically expect 50% buildup and 50% penetration when the anodize is built up. As a .“Sealing Method fr Anodizing Aluminium and Hard Anodizing and Test For Seal Quality Of Aluminium Dr. Xavier Albert Ventura, Laboratory of Electrochemical Research & Development, Integral . In the porous layer the coating relation has a value of l.35 to l.46 due to the existing competitive effect of dissolution against that of oxide .Dissolve 1 gm of Aluminum Blue 2LW Dye*** in 50 ml of Distilled water or DI water. The pH of the dye test solution shall be adjusted to 5.0(plus minus 0.5) . does disappear to leave a clear bear aluminum spot the seal has failed the test. 4.4 Apply a drop of dye solution to the test area and allow it to remain for 5 mins
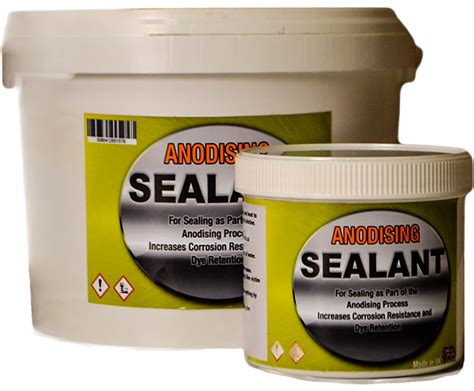
The Anodizing Process in 4 Steps. Step 1. Pre-treatment: Before anodizing, the aluminum part undergoes cleaning and degreasing to rid the surface of contaminants. Step 2. Electrolytic Process: The prepared aluminum piece acts as the anode in an electrical circuit. Submersion in an acid electrolyte bath and the application of electric current release oxygen, which combines .Ensuring your parts are sufficiently finished to withstand environmental conditions is a critical consideration for every product. And among the most popular methods of environmental protection is sulfuric acid anodizing. There are several types of anodizing, and the Mil-PRF-8625 specification lays out the different methods: Type I, Type II and Type III. This article focuses on .Type II anodizing (room temperature) gives an anodized layer of .0002″ to .001″ (half which is grown into the surface and half out of the surface). Parts anodized will become slightly larger by about .0005″. Type III (hard coat) anodizing is done at much colder temperatures and at higher current densities and can reach thick nesses of .Anodizing (Guidelines ˚ r direct current method) . Mainly guideline values, list is only a recommendation which is not binding. We also recommend preparing test samples before final application. Processing steps G.AL C170R, G.AL C190R, G.AL C210R, G.AL C210E, G.AL C210 DYNAMIC, . 50% HNO 3–solution, + 2,5% HF Duration 6 - 20 seconds .
w123 compression test
wabco air compresser testing isx
Epic7, an anime mobile RPG developed by indie Korean studio Super Creative. At its core, Epic7 is a really basic turn-based game with awesome skill effects and enduring anime art. Looking deeper, there is actually quite an epic fantasy setting and a variety of unique playable characters each equipped with stylish skills.
anodizing seal test 35 or 50|anodized aluminum test